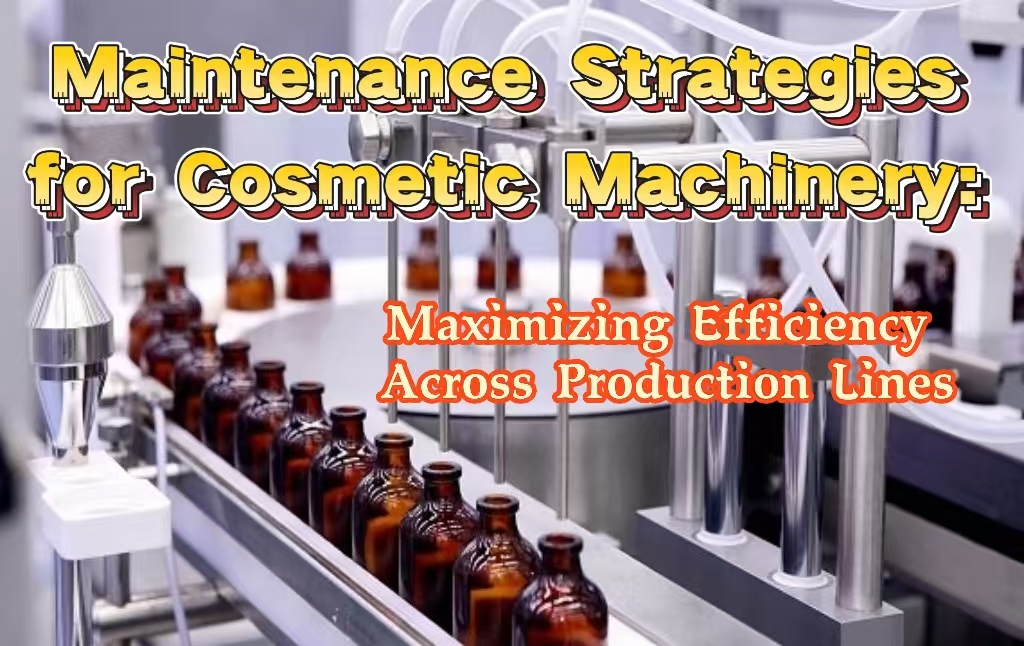
In the competitive cosmetics industry, the reliability of cosmetics machines directly impacts productivity, product quality, and profitability. From cream making machines and liquid soap mixers to integrated filling capping labeling machines, every component of a cosmetic production line demands meticulous care to combat wear, contamination, and operational inefficiencies. This guide explores best practices to extend equipment lifespan.
1. Customized Maintenance for Key Cosmetic Production Line Components
Modern cosmetic production lines integrate diverse systems, each requiring targeted upkeep:
- Cream Making Machines:
- Monitor homogenizer blades and heating elements for residue buildup, which can alter emulsion viscosity.
- Conduct weekly inspections of jacketed vessels to prevent coolant leaks in temperature-sensitive formulations.
- Liquid Soap Mixers:
- Clean agitator shafts and stator-rotor assemblies post-use to avoid soap residue hardening.
- Use non-abrasive cleaners on stainless steel surfaces to maintain hygienic mixing conditions.
- Filling Capping Labeling Machines:
- Replace worn nozzle tips and capping heads to ensure precise fill volumes and airtight seals.
- Calibrate labeling sensors monthly to prevent misalignment in high-speed packaging.
Brands like Granda Machinery design modular systems with quick-disconnect parts, simplifying maintenance without halting entire production lines.
2. Hygiene Protocols to Safeguard Product Integrity
Cosmetic machinery, especially equipment handling creams or liquid soaps, is prone to microbial growth. Implement:
- Post-Process Flushing: Use food-grade solvents in liquid soap mixer tanks to eliminate alkaline residues.
- Steam Sterilization: Apply to cream making machine pipelines and filler nozzles for allergen-free production shifts.
- Dry-Run Cycles: Remove moisture from filling capping labeling machines to prevent label adhesive failure.
Granda’s CIP (Clean-in-Place) compatible systems minimize manual intervention, aligning with FDA and EU Cosmetics Regulation standards.
3. Predictive Maintenance for Downtime Prevention
Leverage technology to anticipate failures:
- Vibration Sensors: Detect imbalance in liquid soap mixer motors or misaligned filling machine conveyors.
- Thermal Cameras: Identify overheating in cream making machine heating zones before burnout occurs.
- IoT Dashboards: Monitor real-time data from Granda’s smart-enabled machines to schedule part replacements proactively.
4. Operator Training for Optimal Machine Handling
Human error remains a leading cause of equipment stress. Train teams to:
- Avoid overloading liquid soap mixers beyond rated viscosity capacities.
- Use manufacturer-approved settings for cream making machines to prevent motor strain.
- Follow lockout-tagout (LOTO) protocols during filling capping labeling machine adjustments.
Granda supplements its machinery with interactive training modules, reducing operational risks.
5. Partner with OEMs for Tailored Support
Generic maintenance plans often overlook niche requirements of cosmetic production lines. Collaborate with OEMs like Granda for:
- Brand-specific spare parts (e.g., cream mixer seals, labeling machine sensors).
- Lifetime access to updated maintenance manuals and troubleshooting guides.
- On-site audits to optimize line-wide efficiency.
Conclusion
A holistic maintenance strategy—combining precision cleaning, predictive analytics, and OEM expertise—can elevate the performance of cosmetics machines while cutting lifecycle costs by up to 30%. As formulations grow more complex, investing in robust equipment like Granda’s cream making machines and liquid soap mixers ensures adaptability to evolving industry demands.
Prioritize longevity; your production line’s reliability is the foundation of brand trust.
(Word count: 498 | Keywords: cosmetics machines, cosmetic production line, cream making machine, liquid soap mixer, filling capping labeling machine, OEM, predictive maintenance, hygiene protocols, Granda)